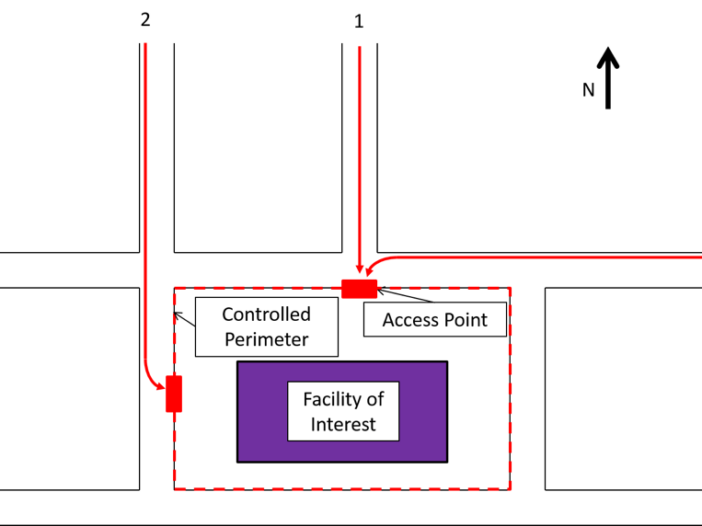
by Timothy Sisson, P.E.
Physical security requirements often include protection against a vehicle ramming threat, where an aggressor attempts to attack a facility by crashing a vehicle through the lobby or loading dock, or by breaching a controlled perimeter around the facility. These threats can be countered by anti-ram vehicle barriers, such as bollards, concrete planters, fences, and ditches/berms.
But how do you choose an anti-ram vehicle barrier? The answer is two-fold: 1) perform a vector analysis to determine the probable threat vehicle velocity at impact and 2) use published standards to specify a rating for the barrier.
A vector analysis requires the following:
- Vehicle weight
- Maximum acceleration
- Friction coefficient between the tires and roadway
- Possible attack route(s)
The maximum acceleration of a vehicle typically ranges between 6 ft/s2 and 11 ft/s2. The acceleration may be increased if the attack route includes the vehicle going down a hill. The friction coefficient depends on road and tire conditions. It ranges between 0-to-1 with 0.6 typically used, however, using 1 is a conservative assumption.
The figure below shows a few examples of possible attack routes at access points around a controlled perimeter. In the figure, Attack Route 1 has a straight approach to the access point, while Attack Routes 2 and 3 are parallel to the access points and require the attacker to turn into the barrier before impact.
Attack Route 1 results in the highest impact velocity because the threat vehicle can continue to accelerate until impact. Attack Routes 2 and 3 limit the velocity at impact because the threat vehicle’s turning radius into the barrier is limited by the coefficient of friction between the tires and the road. If the turn is taken too quickly, the car will skid out of control.
Once the velocity at impact has been calculated, a barrier rating can be specified. At the moment, there are two primary standards used in the United States to rate anti-ram vehicle barriers: ASTM F2656 (F2656) and DoS SD-STD-02.01 (DoS). The DoS SD-STD-02.01 rating system is being phased out and to be replaced by ASTM F2656, but many existing anti-ram vehicle barriers have been tested and rated according to the DoS standard. Both standards rate barriers based on the weight of the vehicle, the velocity at impact, and the allowable penetration.
F2656 provides barrier ratings for multiple vehicle sizes ranging from sedans to heavy goods vehicles (e.g., dump trucks and semi-trailers), however, a common rating is for medium duty truck (M), which corresponds to the DoS “K” rating for a 15,000-lb vehicle weight. There are three (3) “M” ratings:
- M30
- M40
- M50
Which stands for a medium duty truck (M) with a velocity of 30, 40, and 50 mph at impact. These are equivalent to the DoS “K” ratings:
- K4
- K8
- K12
Which also represents a medium duty truck (15,000 lb) with a velocity of 30, 40, and 50 mph at impact.
The penetration rating is also similar between the two (2) documents. F2656 uses the following:
- P1 (less than or equal to 1 m (3.3 ft))
- P2 (1.01 m to 7 m (3.31 ft to 23.0 ft))
- P3 (7.01 m to 30 m (23.1 ft to 98.4 ft))
While the latest DoS rating system assumes a penetration of no greater than 1 M (i.e. a P1 in the ASTM system), previous versions used what was termed “L” ratings, as follows:
- L3 (less than 0.91 m (3 ft))
- L2 (0.91 m to 6.1 m (3 ft to 20 ft))
- L1 (6.1 m to 15.2 m (20 ft to 50 ft))
Obviously a barrier with a lower rating will cost less relative to a higher rated barrier. Performing a vector analysis may show that a K4 (or M30), rather than a K12 (M50), rated barrier is required. In addition, controlling the available attack routes can significantly reduce the barrier requirements by limiting the possible threat vehicle impact velocity. By thoughtfully approaching the rating requirements for anti-ram barriers, project costs can be managed so that the pool of available resources are used where they can best improve the safety and security of the facility and it’s occupants.